The Role of Production Monitoring Software in Achieving Lean Manufacturing Goals
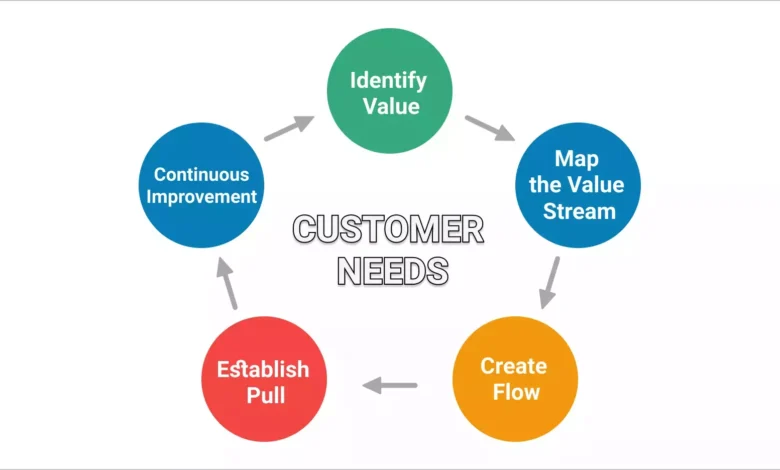
The competitive realm of manufacturing requires an unparalleled level of efficiency and agility, and innovative solutions are deeply valued. There is no room for error. ‘Lean’ manufacturing is an approach defensively deployed by firms across industries to mitigate waste without undermining productivity, quality, or safety. It is in the scope of lean manufacturing that production monitoring software has emerged, giving manufacturers the tools to analyze and optimize their operations to the highest degree possible. This type of software supports swift decision-making and process refinement, thus unleashing unparalleled value, realizing the objectives of lean manufacturing, and achieving growing success.
The Power of Real-Time Data
Production monitoring software thrives on its ability to deliver granular, real-time data across all production facets, transforming raw numbers into actionable insights. This ability ensures that decision-makers have instant access to cycle time, throughput, and inventory levels, fostering a rapid comprehension of production dynamics. By harnessing the power of production monitoring software for lean manufacturing, manufacturers gain the tools to synchronize their operations with lean objectives, enhancing efficiency and performance. Real-time data helps identify and address inefficiencies quickly and facilitates formulating proactive strategies that align with lean principles, such as just-in-time production and total quality management.
Facilitating Waste Reduction
Lean manufacturing’s key tenet is waste elimination, which includes overproduction, excess inventory, and defects. Through the use of monitoring software, companies are able to track the levels of various resources being used and pinpoint areas that can be optimized or reduced, thereby minimizing wastage. Businesses can implement processes that facilitate resource allocation towards value-adding activities after making precise calculations. Such increased productivity not only minimizes costs but also improves product quality due to lower production variability and reduced production inconsistencies, leading to higher customer satisfaction and a better competitive edge in the market.
Enhancing Resource Utilization
Efficient consumption of resources is crucial for the success of lean manufacturing. Production tracking software connects various systems and machines, offering visibility into their performance and usage. Such insights aid managers in improving resource distribution and time scheduling, minimizing downtime, and maximizing business output. Analytics-driven planned maintenance reduces unscheduled outages. The outcome is a more efficient production cycle that fully uses every asset, fulfilling Lean’s maximizing value objective.
Improving Communication and Collaboration
As augmented by production monitoring tools, the transparency afforded by such software greatly aids effective communication and collaboration as well as the sustainment of a lean culture. Stakeholders, from the factory floor to the executive suite, can access production data in real-time, which enables discussions about operational issues and their potential solutions. This assistance permits teams to collaboratively address possible concerns or refine processes, thereby building cultural cohesion anchored in continuous improvement. Information democratization guarantees that all team members are educated and involved, leading to enhanced opportunities to foster innovation and problem-solving.
Enabling Continuous Improvement
In the lean approaches, continuous improvement plays a central role, which is further accelerated by the use of production monitoring software. The software has derived insights in the form of advanced analytics, which offers a detailed evaluation of the work done in comparison with predefined KPIs to show the value of changes that have been made. This feedback loop enables iterative shifts to be made that progressively refine operations. Through sustained efforts, companies imbue their culture with a commitment to excellence, which leads to consistently increased operational efficiency and quality levels.
Facilitating Proactive Problem Solving
Skillful problem-solving in a lean paradigm is proactive in the sense that it relies on anticipating disruptions instead of waiting for them to occur. Production monitoring software augments this capability with real-time alerting features that identify patterns likely to signal emerging issues. These patterns can often be dealt with before they escalate into substantial concerns, allowing production teams to maintain an uninterrupted flow. Such a stance protects against losses and fosters the culture of unyielding dedication to uptime, quality output, and consistent value—dimensions essential to lean manufacturing goals.
Customization and Scalability for Diverse Needs
From specialized workshops to large and intricate factories, the diversity in manufacturing landscapes is observable. Customization and scalability are two traits that make production monitoring software stand out, as it can be adapted to suit various environments and requirements. These systems can efficiently work with different setups, whether they are local systems or connected to global networks, to maintain consistent accuracy that meets lean goals. Their adaptability guarantees that regardless of size or complexity, all organizational entities are able to benefit from advanced production monitoring systems.
Supporting Data-Driven Decision Making
As with any lean system, production monitoring software is needed to support decisions with evidence. The software makes complex data sets easier to understand through visual data representations. Manufacturers are able to interpret data strategically through visual dashboards and reports. Furthermore, algorithm-driven solutions alongside artificial intelligence are enabling sophisticated predictive analytics, paving the way for businesses to sift through ever-growing data volumes to make powerful business decisions. Machine learning and artificial intelligence can examine historical data to tailor algorithms that evaluate prospective market trends alongside competitive driving forces, allowing businesses to streamline operations. This must be done before undergoing any fundamental changes. Undergoing lean changes becomes effortless and ceaseless by enabling companies to pivot and realign swiftly through advanced, simple interfaces while continuously fueling lean objectives.
Mitigating Risk and Ensuring Compliance
Today’s manufacturing environments must have strong risk management and regulatory compliance. Production monitoring software provides this functionality by tracking deviations and maintaining audit trails in real-time. From an overarching view, manufacturers can confirm that they comply with industry and regulatory requirements. This assists in correcting operational inconsistencies, mitigating liability, maintaining product integrity, and preserving product quality. Production monitoring software integrates compliance within lean frameworks, protecting operations and boosting trust and responsibility.
Conclusion
Production monitoring software emerges as an indispensable tool in pursuing lean manufacturing excellence. It enables real-time data acquisition, fosters transparent communication, and supports continuous improvement—cornerstones of the lean philosophy. This technology’s flexibility and adaptability allow diverse manufacturing sectors to capitalize on data-driven insights and ensure efficient resource usage. As the industry evolves, lean manufacturing, powered by production monitoring software, sets the stage for sustainable growth and success, equipping companies to meet future challenges with confidence and agility.