The Latest Innovations in Diesel Engine Technology
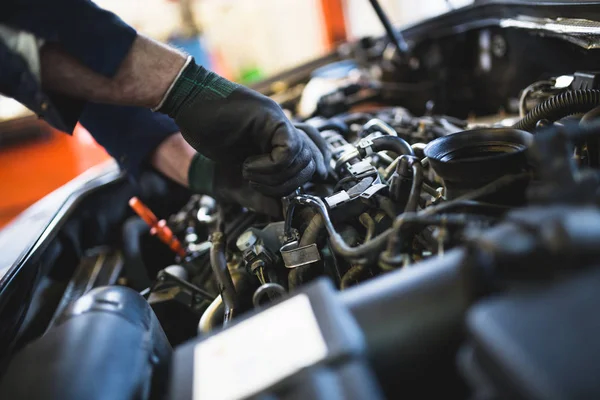
Several attempts and triumphs have been made over the past few decades to increase the overall effectiveness of the diesel engine. The majority of these adjustments affect how the engine’s fuel and oxygen mixture ignites to produce power. The energy required to start the engine finally comes from this mixture.
Making as many repair and rebuilding operations in-house as possible is what we believe to be the best way to deliver dependable and timely service and maintain our quality. Here at Pro Automotive & Diesel, we offer everything you may need for your vehicle
Since their invention, diesel engines have advanced significantly, and manufacturers have recently pushed the limits of innovation to make them more effective, clean, and sustainable. The diesel engine industry has risen to the challenge, introducing ground-breaking technologies that pave the way for a greener future as environmental concerns and strict emission regulations take center stage.
Here are some of the latest innovations in diesel engine technology:
Technology for Clean Diesel
Clean diesel technology has advanced significantly as a result of environmental consciousness. Diesel engine manufacturers have implemented sophisticated exhaust after-treatment systems to address the issue of harmful emissions. Selective Catalytic Reduction (SCR) is a prime example of an innovative system harnessing a distinctive catalyst to transform toxic nitrogen oxides (NOx) into benign nitrogen and water vapor. Diesel Particulate Filters (DPF), in addition to SCR, have grown in popularity. DPFs significantly lower the amount of airborne pollutants by capturing and removing particulate matter from exhaust gases.
High-Pressure Injection Methods
Recent advances in high-pressure injection systems have revolutionized diesel engines, which depend heavily on fuel injection systems for engine efficiency. With the help of electronic unit injectors (EUI) and common rail direct injection (CRDI) systems, precise fuel delivery is made possible, improving combustion efficiency while lowering fuel use and emissions.
Downsizing and Turbocharging
The concept of downsizing diesel engines while incorporating turbocharging technology has gained momentum. Manufacturers can achieve enhanced fuel efficiency by reducing engine displacement and utilizing turbochargers without compromising power output. Smaller engines with turbochargers generate higher torque at lower RPMs, making them ideal for heavy-duty applications and reducing the engine’s environmental impact.
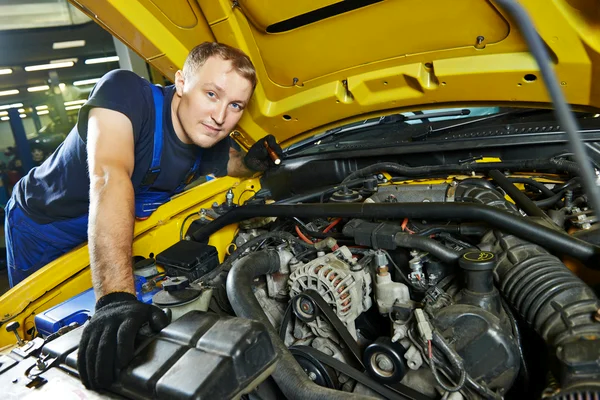
Diesel Hybrid Systems
Hybrid powertrains, which combine the benefits of electric motors and diesel technology, have become a new ally for diesel engines. Hybrid diesel systems have better fuel efficiency, fewer emissions, and less noise. In start-stop traffic, where the electric motor can handle low-speed driving, saving fuel and lowering exhaust emissions, the combination of an electric motor and a diesel engine enables seamless power delivery.
A Better Use of Materials and Design
Engineers have turned to cutting-edge materials and engine design to pursue efficiency. Engine components are increasingly made of lightweight materials like aluminum and advanced composites to reduce overall weight and improve performance. Furthermore, advanced design methods that optimize combustion processes for greater fuel efficiency include computational fluid dynamics (CFD) simulations.
Recovery of Waste Heat
Diesel engines are infamous for producing a lot of waste heat while running. Engineers have come up with inventive ways to gather this waste heat and convert it into useful energy, though. Systems for recovering waste heat can help the engine’s power output or convert heat energy into electricity, improving thermal efficiency and lowering fuel usage.
Modernized Engine Management Techniques
Diesel engines have benefited from the digital revolution through sophisticated engine management systems. These systems, outfitted with various sensors and actuators, continuously monitor engine performance and adjust real-time parameters. Furthermore, artificial intelligence algorithms tailor engine performance based on various variables, including load, speed, and driving circumstances. With the help of this intelligent technology, combustion is more efficient, emissions are decreased, and overall performance is improved.
Prevention-Based Maintenance
Diesel engines now have access to predictive maintenance thanks to Internet of Things (IoT) integration. These engines can inform maintenance teams about their health status in real-time, enabling them to take proactive steps to avoid breakdowns and downtime. Predictive maintenance reduces repair costs, lessens environmental impact, and boosts reliability.
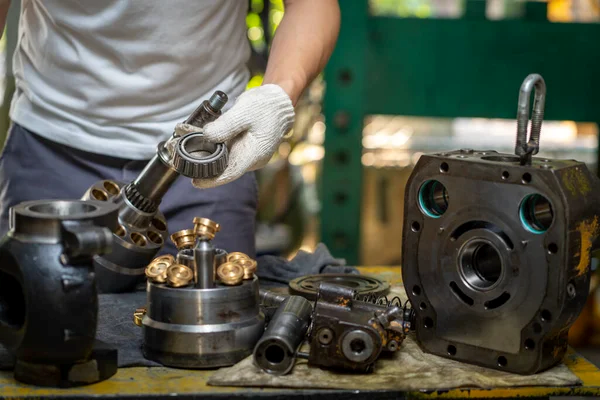
3D Printing
The introduction of 3D Printing has changed several industries, including the production of diesel engines. Engine parts that are lighter yet more robust can now be created using printed components with complex designs and unique geometries. In addition to speeding up production, 3D Printing also minimizes waste, making it a sustainable choice.
The diesel engine industry is currently going through a period of rapid innovation and environmental challenge adaptation. Manufacturers are integrating digital solutions, enhancing engine designs, and investing in cleaner technologies to increase performance and lower emissions. Diesel engines are well-positioned to continue playing a crucial role in our transportation and industrial sectors while contributing to a greener and more sustainable future thanks to advancements in clean diesel technology, hybrid systems, and waste heat recovery. These developments will undoubtedly influence the development of diesel engine technology, bringing us closer to a cleaner and more productive tomorrow.