Transportation Planning and Scheduling: Strategies for Optimizing Logistics
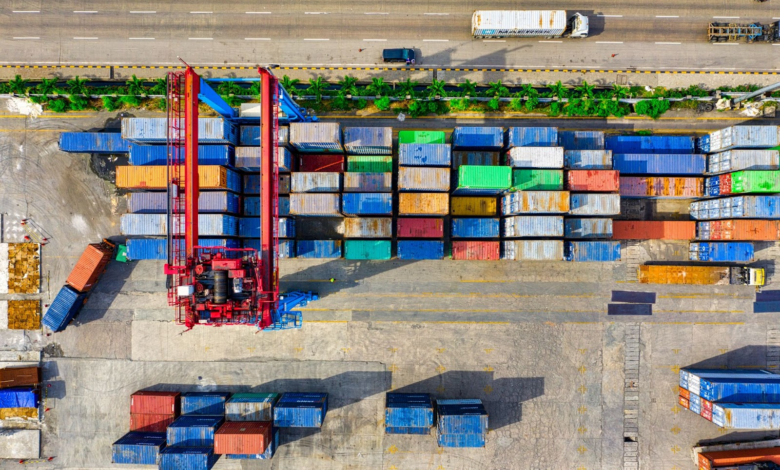
Logistics planning and scheduling are essential. To meet modern supply chain demands, organizations must optimize their transportation processes. This article discusses logistics planning and scheduling and offers tips for improving them.
The Importance of Planning and Scheduling in Logistics
Logistics operations require effective transportation planning and scheduling. Companies may cut expenses, idle time, and customer happiness by carefully planning routes, shipment amounts, and delivery times. Planning maximizes vehicle, driver, and fuel use for enterprises. It enables them to respond swiftly to changing market conditions, such as unforeseen delays or fluctuations in demand.
Here are some strategies for effective transportation planning and scheduling:
1. Route Optimization
Utilize advanced routing software that considers traffic conditions, distance, and delivery time windows. Consolidate shipments to minimize the number of trips and optimize vehicle capacity. Consider alternative routes or transportation modes to bypass congested areas or avoid tolls.
2. Load Balancing
Analyze historical data and demand patterns to distribute loads evenly across vehicles.
Optimize load sequencing to minimize travel time and improve efficiency. Use load optimization software to determine the best arrangement of items within the vehicle, considering weight distribution and fragile goods.
3. Collaborative Planning
Partner with customers, suppliers, and logistical providers. Work with industry peers to cut costs. Implement real-time communication systems to facilitate quick decision-making and resolve issues promptly.
Equipment Reliability: A Key Component in Logistics
Reliable transportation equipment is essential for smooth logistics operations. When vehicles or equipment break down unexpectedly, it can lead to disruptions in delivery schedules, increased costs, and dissatisfied customers. Regular maintenance and timely repairs are critical to prevent breakdowns and minimize downtime.
Well-maintained vehicles and equipment contribute to increased reliability, fuel efficiency, and driver safety by implementing preventive maintenance programs. Companies can reduce the risk of unexpected failures and ensure the availability of their assets when needed.
Regular maintenance examples enhance equipment reliability in logistics:
1. Preventive Maintenance
Routine inspections and maintenance are integral to effective planning and scheduling in logistics operations. By implementing preventive maintenance programs, companies can proactively address potential issues before they escalate into major problems, aligning with the goals of planning and scheduling for optimized logistics.
For instance, regular oil changes and filter replacements prevent engine damage and improve fuel economy. This reduces operational expenses and environmental impact.
2. Predictive Maintenance
Leveraging advanced technology such as sensors and data analytics allows companies to monitor equipment performance in real time and identify signs of potential failure.
For example, predictive maintenance can help detect abnormal vibrations in a vehicle’s braking system, indicating the need for immediate attention to avoid safety risks and costly repairs.
3. Regular Inspections
Conducting routine inspections ensures that equipment is in proper working condition and compliant with safety standards. For instance, regular tire inspections, including checks for wear, damage, and proper inflation, can prevent blowouts and accidents while improving fuel efficiency.
4. Timely Repairs
Maintaining and repairing equipment immediately reduces downtime and maintains readiness. For example, promptly fixing a faulty cooling system in a refrigerated truck can prevent spoilage of perishable goods and maintain product integrity during transportation.
By prioritizing equipment reliability, companies can experience several benefits in logistics operations. Reliability boosts operational efficiency, cost savings, and customer pleasure. It makes logistics workers and drivers safer.
Maintenance Management in Logistics
Maintenance management involves systematically planning, organizing, and controlling maintenance activities to optimize logistics operations. It encompasses various aspects, including scheduling routine inspections, conducting repairs, and managing spare parts inventory.
An effective maintenance management system allows companies to:
1. Tracking Equipment Maintenance History
Companies can track equipment maintenance by documenting maintenance activities, repairs, and inspections. This identifies recurrent issues or components that need frequent attention, allowing preventive maintenance to prevent future breakdowns.
A logistics organization may find that a vehicle’s transmission system frequently fails. By tracking this history, they can plan more frequent checkups or contemplate a preventive replacement.
2. Implementing Proactive Maintenance Measures
Proactive maintenance prevents costly repairs and equipment failure in a good maintenance management system. This includes routine inspections, preemptive part replacement, and manufacturer-recommended preventive maintenance.
Cleaning and calibrating temperature sensors in refrigerated trucks help prevent malfunctions and provide correct temperature management for perishable commodities.
3. Monitoring Key Performance Indicators (KPIs)
MTBF and MTTR are useful indications of maintenance efficacy. By monitoring these KPIs, companies can identify areas for improvement and track the overall reliability of their equipment.
For example, suppose the MTBF of a specific vehicle decreases over time. In that case, it may indicate that maintenance activities need to be adjusted or that a replacement vehicle is necessary to maintain the desired level of operational reliability.
An effective maintenance management system ensures the operational readiness of equipment and contributes to cost control and overall efficiency in logistics operations. By systematically planning and organizing maintenance activities, companies can minimize downtime, reduce the risk of unexpected breakdowns, and optimize the utilization of their assets.
The Impact of Maintenance on Equipment
Regular maintenance significantly extends the lifespan of transportation equipment and enhances its performance. Well-maintained automobiles use less fuel, release fewer emissions, and work more effectively.
This cuts costs and supports sustainability. Such as:
- Regular oil changes and filter replacements can prevent engine damage and improve fuel economy.
- Proper tyre maintenance, including rotation and alignment, ensures optimal traction, reduces wear and enhances safety.
- Scheduled inspections and repairs of braking systems contribute to reliable stopping power and prevent accidents.
The Significance of Plant Maintenance
Plant maintenance is crucial in logistics operations, which encompasses the upkeep of facilities and infrastructure. Neglecting plant maintenance can lead to operational disruptions, safety hazards, and increased costs.
By implementing an effective plant maintenance strategy, companies can:
- Conduct regular inspections and repairs to ensure safe working conditions.
- Upgrade and modernize facilities to accommodate changing business requirements.
- Implement energy-efficient practices to reduce utility costs and environmental impact.
Assessing Reliability in Your Logistics Operations
Conducting reliability assessments helps companies identify potential weaknesses in their logistics operations and develop improvement plans. Here are steps to assess reliability:
- Gather historical data on equipment failures, delays, and maintenance activities.
- Analyze the data to identify trends, recurring issues, and areas for improvement.
- Define key performance indicators (KPIs) such as on-time delivery rate, mean time between failures (MTBF), and maintenance costs.
In Summary
Effective transportation planning and scheduling are vital for optimizing logistics operations. Companies can reduce costs, improve customer satisfaction, and enhance operational efficiency by implementing strategies such as route optimization, load balancing, and collaborative planning.
Moreover, prioritizing equipment reliability through regular maintenance and implementing effective plant maintenance strategies further contributes to seamless logistics operations. Companies can stay competitive in today’s dynamic business landscape by continuously assessing and improving reliability.