Perfecting the Cleanroom: Strategies for Success
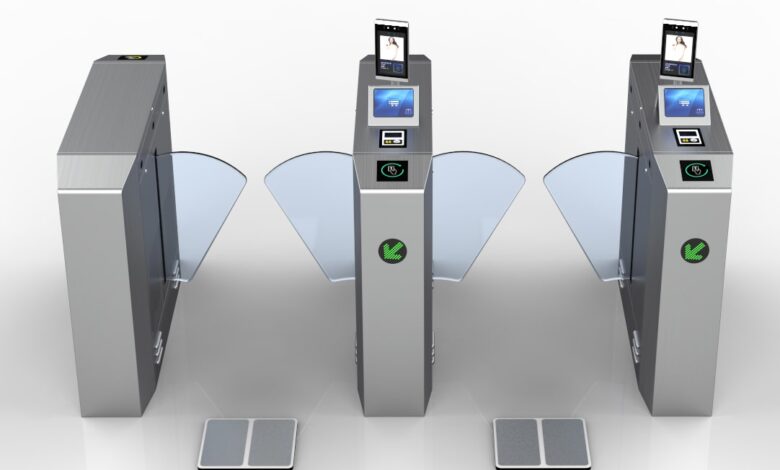
The cleanroom is a critical environment for several industries, from healthcare to pharmaceuticals, to electronics manufacturing. Each industry has its unique requirements, but all have one common goal: to eliminate any form of contamination throughout the production process. With the stakes so high, it’s critical to have strategies in place to achieve and maintain a cleanroom environment. Here are ten strategies to perfect the cleanroom.
1. Develop a Cleaning and Maintenance Plan – A cleanroom needs a systematic cleaning and maintenance plan to maintain a contamination-free environment. This plan should include the frequency of cleaning, use of cleaning products, and the necessary cleaning tools.
2. Train Employees – In addition to having a cleaning plan, employees must be properly trained in cleanroom protocols, cleaning procedures, and contamination avoidance techniques.
3. Regular Monitoring – Monitoring of the cleanroom environment is necessary to ensure that contamination levels are low. Regular monitoring includes checking room temperatures, humidity levels, and air flow.
4. Installation of HEPA Filters – Proper air filtration is an essential aspect of maintaining a cleanroom environment. The installation of High-Efficiency Particulate Air (HEPA) filters helps to remove particulate matter and microorganisms from the environment.
5. Implementing Positive Pressure – The introduction of positive pressure into a cleanroom environment helps to prevent contamination by keeping unfiltered air out of the room, which helps to maintain the integrity of the cleanroom.
6. Designing Equipment with Cleanability in Mind – Equipment used in the cleanroom is prone to contamination. To avoid this, equipment must be designed with cleanability in mind, which means they are easy to dismantle, clean, and reassemble.
7. Proper Gowning – Proper gowning techniques are essential to prevent contamination. This means employees must be dressed in cleanroom gowns, gloves, and footwear when entering the cleanroom.
8. Implementing Segregation Areas – An effective way to control the movement of people in the cleanroom is to introduce segregation areas. This involves having an area where employees can discard their outer clothing before entering the cleanroom.
9. Minimizing the Use of Paper Documents – Paper is a significant source of contamination in the cleanroom. By minimizing the use of paper documents in favor of electronic versions, the risk of contamination is lessened.
10. Implementing ESD turnstile – Electrostatic discharge (ESD) is a severe problem in the cleanroom. Implementing ESD turnstile is an effective way to prevent excessive ESD levels on human bodies from causing damage to sensitive electronic equipment.
In conclusion, perfecting the cleanroom requires a combination of strategies to eliminate any form of contamination throughout the production process. Implementing strategies like a cleaning and maintenance plan, employee training, and regular monitoring creates a system that ensures the cleanroom is always clean and contamination-free. The installation of HEPA filters, positive pressure, and equipment designed with cleanability in mind reinforce the commitment to maintaining a cleanroom environment. Proper gowning, the introduction of segregation areas, minimizing the use of paper documents, and esd turnstile gate system ensure that employees and equipment are free of all forms of contamination. Applying these approaches when developing your cleanroom procedures ensures optimal operation and guarantees sterile, uncontaminated products.