Material Handling in Warehouses: What to Know
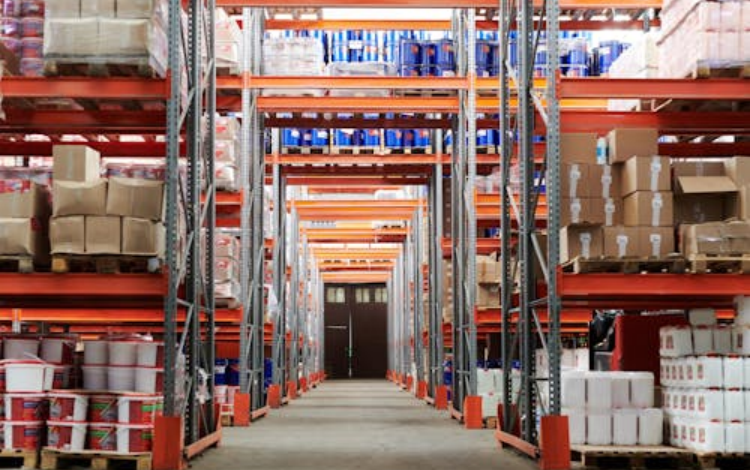
Efficient material handling is at the core of every well-run warehouse. With countless pallets, boxes, and products moving daily, even small errors can lead to inefficiencies or accidents. So, how can warehouses optimize their material handling processes while keeping employees safe? In this article, we’ll take a closer look at the importance of material handling, the tools involved, and practical tips to streamline operations.
What Is Material Handling in Warehouses?
Material handling refers to managing and moving goods within a warehouse (see more here), from receiving inventory to shipping it out. It includes various steps such as lifting, storing, and transporting products, and involves tools, equipment, and processes designed to make these tasks faster and safer.
When done right, material handling improves workflow, reduces inventory damage, and lowers the risk of worker injuries. On the other hand, poor practices can lead to bottlenecks, delays, and higher operating costs.
Key Tools for Material Handling
Warehouses use a mix of manual labor and specialized equipment to handle goods. The tools chosen depend on the warehouse size, product type, and business needs.
1. Forklifts
Forklifts are essential for moving heavy loads quickly across the warehouse. They’re commonly used to stack products on high shelves or transport materials over short distances. However, forklift operators should be trained properly, as misuse can lead to workplace accidents.
2. Conveyor Belts
Conveyor systems are ideal for moving items along fixed paths. They’re commonly used in packing and shipping areas, ensuring products flow smoothly from one station to the next. Conveyors save time and reduce the need for manual lifting.
3. Pallet Jacks
For smaller loads or tight spaces, pallet jacks are a go-to option. While not as powerful as forklifts, they’re easy to use and highly versatile. Electric and manual pallet jacks are great for handling lighter, localized tasks.
4. Racking Systems
Good storage is the backbone of efficient handling. Racking systems maximize vertical space, making it easy to organize products by type, size, or SKU. Selective racking and drive-in racks are popular choices in modern warehouses.
5. Automation Technology
Automated guided vehicles (AGVs), robotics, and automated storage systems are transforming the way warehouses operate. While these options require an upfront investment, they reduce long-term labor costs and improve accuracy.
Best Practices for Warehouse Material Handling
Improving material handling in warehouses is about more than just tools. It requires well-planned strategies, ongoing employee training, and a commitment to safety.
1. Train Warehouse Employees
Untrained workers can easily make costly mistakes or hurt themselves while handling equipment. Regular training ensures they know how to operate tools correctly and follow safety guidelines. This reduces injuries and increases productivity.
Ask yourself: Does everyone on your team know how to lift properly? Something as simple as bending knees instead of the back when lifting reduces strain and helps prevent injuries.
2. Optimize Warehouse Layout
A well-designed layout minimizes unnecessary movement and speeds up material handling. Make it easy for workers to find what they need. Use clear signage, map out paths for forklifts, and keep high-priority items up front.
For example, does it make sense to store fast-moving products at the back? Probably not. Keep high-demand items close to loading areas to save time.
3. Use Technology for Tracking
Inventory management software helps you know where products are at all times. Digital solutions like barcodes and RFID systems reduce errors in inventory counts and speed up retrieval.
Are you still relying on paper logs? Switching to software not only boosts accuracy but also streamlines the entire handling process.
4. Maintain Equipment Regularly
Broken equipment causes delays and increases safety hazards. Set up a schedule for routine maintenance to keep machinery in top shape. This simple step can prevent costly breakdowns and downtime.
5. Reduce Lifting and Carrying
Whenever possible, minimize manual lifting. Provide workers with tools like carts, lifts, or adjustable-height tables to reduce the need for heavy carrying. Ergonomics play a key role in protecting your employees and keeping workflows smooth.
Why Safety Should Always Come First
Material handling in warehouses, something that companies like Raymond Storage Concepts is well versed in, isn’t just about speed—it’s also about safety. Worker injuries disrupt operations and can lead to lawsuits or penalties. Creating a safety-first culture makes a huge difference.
- Provide Personal Protective Equipment (PPE): Helmets, gloves, and safety shoes protect against common hazards.
- Perform Routine Inspections: Identify and fix hazards before they cause accidents.
- Encourage Reporting: Make it easy for employees to report unsafe conditions without fear of retaliation.
Remember, a safe workplace is also a more productive one. When workers feel valued and protected, they’re more motivated to give their best.
Conclusion
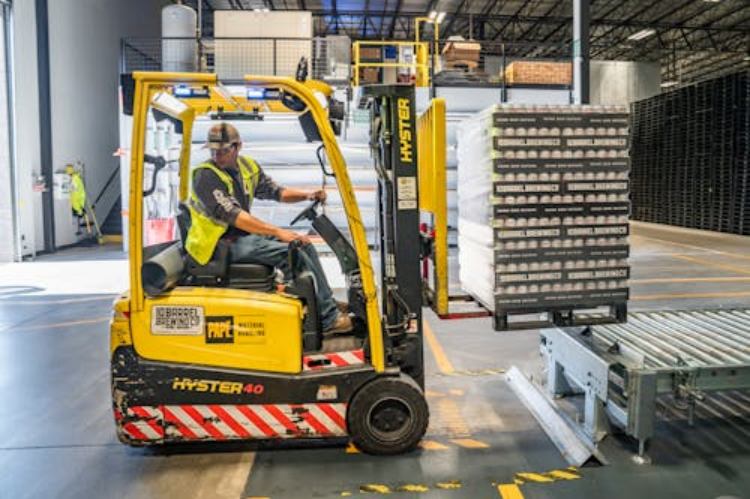
Material handling is a critical factor in warehouse operations, and something that should be handled with the right equipment, knowledge, and safety. By combining the right tools, strategies, and safety practices, you’ll not only improve efficiency but also protect your most valuable resource: your people.
Regular training, smart layout planning, and technology adoption can help you stay ahead in this fast-moving industry. And when challenges arise, a proactive approach keeps your warehouse running like clockwork.