Innovative Techniques for Efficient Edgebanding
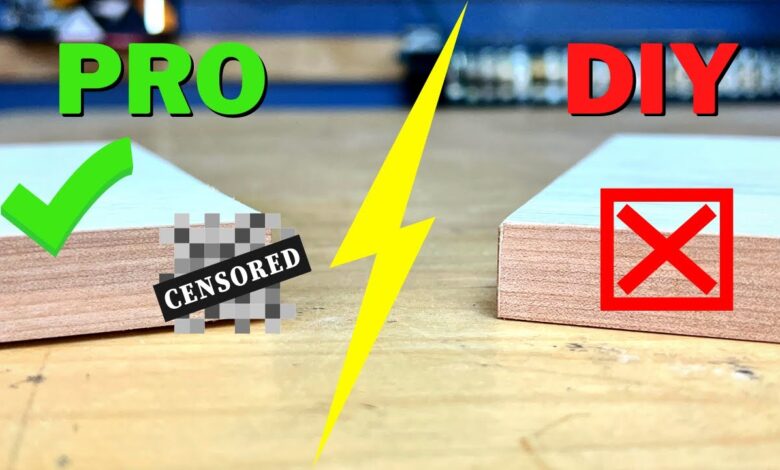
Recent advancements in edgebanding technology have transformed the woodworking industry, introducing solutions that address both the demand for efficiency and the need for outstanding visual appeal. Today, the edge detail on a finished product is much more than a functional necessity; it is a defining element of craftsmanship and quality. With tools like the modern wood trimmer playing a crucial role in achieving precise, clean cuts, the evolution of edgebanding ensures that every edge on furniture and cabinetry is not only seamlessly finished but also highly durable and visually stunning over the long term.
Keeping pace with technological innovation is essential for anyone seeking to remain competitive in the woodworking industry. Emerging trends in edgebanding are not just about faster turnaround; they also enhance product reliability, aesthetic standards, and even environmental stewardship. This article explores the most forward-thinking methods in use today, offering a comprehensive guide to best practices and next-generation technologies that are reshaping project execution and outcomes.
Zero-Joint Technology
Zero-joint technology represents a significant advancement in achieving pristine, seamless edge finishes. This innovative approach eliminates the visible glue lines that can detract from the finished look, ensuring every joint is virtually invisible. As highlighted in this resource, the benefits are more than surface deep—zero-joint edges offer exceptional resistance to delamination and moisture penetration, making them particularly valuable in applications subject to frequent temperature fluctuations or exposure to humidity, such as kitchens and bathrooms. For discerning clients and projects where lasting visual appeal matters, zero-joint technology sets a new standard for edge perfection.
How Zero-Joint Works
At the heart of this method are technologies like laser edgebanding, which replaces traditional adhesives with a high-intensity laser that fuses a heat-sensitive layer on the edgeband to the substrate’s edge. This creates a single, flawless surface with no need for additional glue. The absence of a glue line not only improves aesthetics but also forms a seal that prevents water and debris from breaking the bond over time, extending the life and maintaining the beauty of the finished product.
Benefits
- Achieves seamless joints that are virtually invisible to the naked eye, enhancing the look of cabinetry and furniture.
- Improves performance in environments exposed to steam, water, or intense cleaning, preventing typical issues like swelling or peeling.
- Minimizes the need for future repair or maintenance, delivering better value and peace of mind to clients.
PUR Adhesives
The rise of Polyurethane Reactive (PUR) adhesives has been a pivotal development in edgebanding techniques. PUR adhesives are a revolutionary alternative to traditional EVA glues, providing extraordinary strength and flexibility across a range of applications. The chemical bond created by PUR adhesives not only holds the material but also resists hot water, steam, and physical wear, providing furniture and fixtures with unmatched longevity, even under heavy use or tough cleaning routines.
Key Properties of PUR Adhesives
One of the reasons PUR is so effective is its unique curing process. When exposed to air, the adhesive reacts with ambient moisture, developing a dense, resilient bond. This not only ensures structural integrity but also allows for significantly thinner application lines, so the glue all but disappears into the edge, keeping lines crisp and clean. For any application demanding strength and subtlety, PUR is the adhesive of choice.
Applications
High-traffic residential spaces, such as kitchens and bathrooms, require edge durability.
Commercial furniture in offices, hotels, and public spaces, where resistance to wear and tear is a must.
Laboratory and healthcare environments require robust, easy-to-sanitize surfaces.
Automated Edgebanding Machines
Automation is redefining workflow efficiency in woodworking. These machines are equipped with advanced sensors, intelligent software, and flexible configurations, enabling operators to adjust settings for various panel sizes, shapes, or materials with minimal intervention, often through a straightforward user interface.
Modern Solutions and Capabilities
Advanced automation enables seamless switching between edgebanding materials, ranging from rigid woods to pliable PVC or ABS, and vice versa, significantly reducing downtime and enhancing overall throughput. Additional features, such as automatic feeding, trimming, corner rounding, and even cleaning, ensure that each piece meets rigorous standards of uniformity and quality, making these machines indispensable for manufacturers handling large volumes or bespoke custom orders alike.
Digital PVC Edgebanding
Digital PVC edgebanding is unlocking new creative possibilities by leveraging high-resolution printing technology. Through digital means, manufacturers can precisely match colors, woodgrains, and textured finishes—or even apply branding and complex graphics—directly onto edgebands. This method is ideal for custom projects, retail environments, or anyone seeking to add a personalized touch to otherwise standard furniture elements.
Industry Implementation
Trailblazers are leading the way in integrating digital PVC printing into the manufacturing process. This process enables rapid prototyping and short production cycles, making it an ideal option for custom jobs and reducing the inefficiencies of traditional edgebanding. Intricate, photorealistic designs or subtle, repeated patterns can be produced without excess material waste, thereby satisfying diverse aesthetic demands and supporting sustainable manufacturing goals.
Sustainable Edgebanding Practices
Sustainability is now a top priority for both woodworking professionals and consumers. The edgebanding industry is responding with inventive approaches that minimize environmental impact without sacrificing finish or durability. Modern sustainable practices are centered on the responsible sourcing of materials, the use of more environmentally friendly adhesives, and the reduction of waste throughout production cycles.
Eco-Conscious Materials and Processes
- Utilizing edgebands made from recycled content or fast-growing, renewable resources, helping to conserve natural materials and reduce landfill waste.
- Switching to water-based, low-VOC adhesives that reduce harmful emissions, improve indoor air quality, and contribute to a safer manufacturing environment for workers.
- Adopting circular production approaches, with systems designed to recapture, repurpose, or recycle off-cuts and excess materials, improves overall efficiency and reduces costs.
Benefits for Modern Woodworkers
Beyond aligning with customer expectations for green, responsible products, these sustainable approaches often translate to operational savings by streamlining resource use and minimizing waste. Woodworkers embracing these methods can also tap into new eco-conscious markets, securing a strong brand reputation and establishing themselves as industry leaders in environmental stewardship. The future of edgebanding lies in the intelligent integration of digital, automated, and sustainable methods, ensuring the highest levels of quality, efficiency, and environmental care.