Customizing Medical Injection Molding for Specific Applications
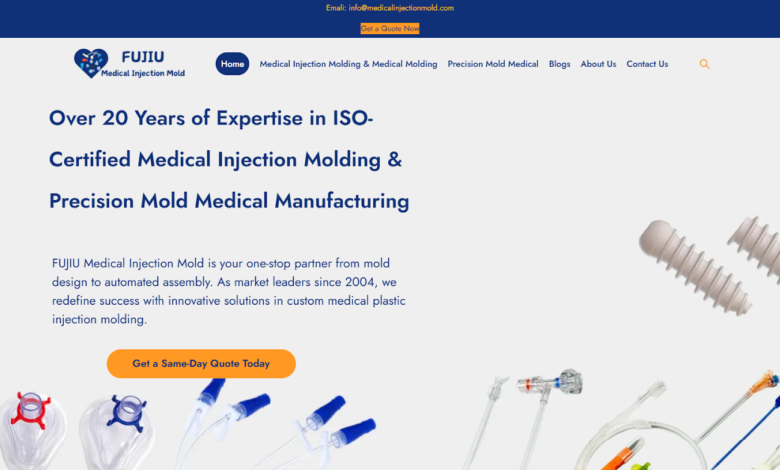
Customizing medical injection molding is essential to meet the unique demands of various medical applications. The healthcare industry requires components that not only meet stringent regulatory standards but also function under specific conditions, such as exposure to extreme environments, sterilization processes, or the need for biocompatibility. The ability to tailor injection molding processes to specific needs ensures that medical devices and equipment perform optimally, safely, and consistently.
Material Selection for Specific Applications
One of the key elements in customizing medical injection molding is selecting the right material for each application. The choice of material depends on several factors, such as biocompatibility, mechanical properties, and the part’s intended use. Some common materials used in medical injection molding include:
- Polypropylene (PP): Often used for its chemical resistance, low cost, and ease of sterilization. Ideal for applications like drug delivery systems and packaging.
- Polycarbonate (PC): Known for its transparency and high impact resistance, making it suitable for medical devices that require clarity, such as surgical instruments or diagnostic equipment.
- Polyethylene (PE): Chosen for its flexibility and biocompatibility, often used in packaging or components for implants.
- Medical-Grade Silicone: Used for components that need to be flexible and resistant to high temperatures, such as catheters, seals, and tubing.
For more specialized applications, advanced materials such as biodegradable polymers, bioresorbable plastics, and thermoplastic elastomers (TPE) can also be customized to meet the specific functional, mechanical, or environmental requirements of the medical devices. FUJIU Medical Injection Mold offers a comprehensive range of these materials, ensuring that each is selected to meet the precise needs of their clients’ medical device applications, while maintaining high standards of performance and regulatory compliance.
Designing for Functionality and Fit
The design phase of medical injection molding must align closely with the specific functionality of the end product. Medical devices often require components that fit precisely within a larger system, such as implants, diagnostic tools, or surgical devices. Precision mold medical allows for the creation of highly detailed and customized molds that cater to these needs. Customization at this stage may involve:
- Complex Geometries: The ability to create parts with intricate shapes or fine details that meet specific design requirements, such as micro-holes, thin walls, or delicate surfaces.
- Multi-material Molding: For some applications, it may be necessary to combine different materials in one part. Multi-shot injection molding allows the integration of different material types or colors in a single process. For example, combining rigid materials with soft, flexible ones for medical seals or gaskets.
- Overmolding and Insert Molding: These techniques are used when a part requires multiple material layers or when other components, such as electronics or metal inserts, need to be integrated into the plastic parts. This is common in devices like sensors or monitors.
Sterilization and Safety Considerations
In medical applications, ensuring that components can withstand various sterilization processes is crucial. Customizing the injection molding process to suit sterilization methods such as autoclaving, gamma radiation, or ethylene oxide (EtO) sterilization is an important step. The selected material must be compatible with these sterilization techniques without compromising the material’s integrity, strength, or function.
In addition, biocompatibility must be carefully considered. For devices that will be in contact with the human body, such as implants, syringes, or catheters, the materials must pass rigorous testing to confirm they do not cause adverse reactions. Custom formulations can be developed to meet these requirements.
Tailoring for Performance in Harsh Environments
Medical devices often operate under challenging conditions, including exposure to extreme temperatures, pressure, or chemical substances. Customizing the injection molding process can ensure that the parts perform optimally in these environments. For instance:
- High-temperature applications: Components used in sterilization equipment, surgical tools, or medical diagnostic devices may need to withstand high temperatures without deforming. High-temperature resistant materials such as polyphenylene sulfide (PPS) or polyetheretherketone (PEEK) can be used.
- Chemical resistance: For medical equipment that is exposed to aggressive chemicals or cleaning agents, materials with enhanced chemical resistance, such as certain grades of polyethylene or polypropylene, can be customized for improved durability.
- Impact resistance: Medical devices used in trauma care or emergency situations, such as splints, must be designed to absorb impacts and prevent damage. Materials with enhanced impact resistance, like polycarbonate, are used for these applications.
Scale and Production Flexibility
Customizing medical injection molding also involves tailoring the production process to suit the scale of manufacturing. Depending on the production volume, the complexity of the mold, and the material used, manufacturers may adjust processes to meet the specific needs of the application:
- Small-batch Production: For niche medical devices or prototypes, small-batch injection molding may be necessary. This allows for quicker turnarounds and more flexibility in design adjustments.
- High-volume Production: When a medical device requires high-volume manufacturing, such as syringes or medical packaging, the injection molding process can be customized for efficient, cost-effective mass production while maintaining the strict quality standards required for medical use.
Integration with Regulatory Requirements
Medical components must comply with various regulations and certifications, such as the FDA’s 21 CFR Part 820, ISO 13485, and CE marking in Europe. Customizing the medical injection molding process means ensuring that every aspect of production, from material selection to manufacturing practices, adheres to these regulatory requirements. This includes maintaining detailed documentation of design changes, testing results, and production batches to ensure traceability and compliance.
Custom Solutions for Specific Devices
Finally, customizing medical injection molding also involves tailoring the process to fit the specific needs of particular medical devices. Some examples include:
- Implants and Prosthetics: Custom molds may be required to fit the contours of a patient’s body, ensuring the prosthetic or implant provides maximum comfort and functionality.
- Diagnostic Tools: Injection molding may be customized for devices such as blood test kits, diagnostic chambers, or imaging tools. These devices often require precision molding for critical measurements.
- Surgical Instruments: Precision and reliability are critical for surgical instruments such as scalpels, forceps, or tweezers. Customization ensures that these tools are manufactured to meet stringent standards for strength, sharpness, and ease of use.