Cooling of Motor Spindles – A Comprehensive Review
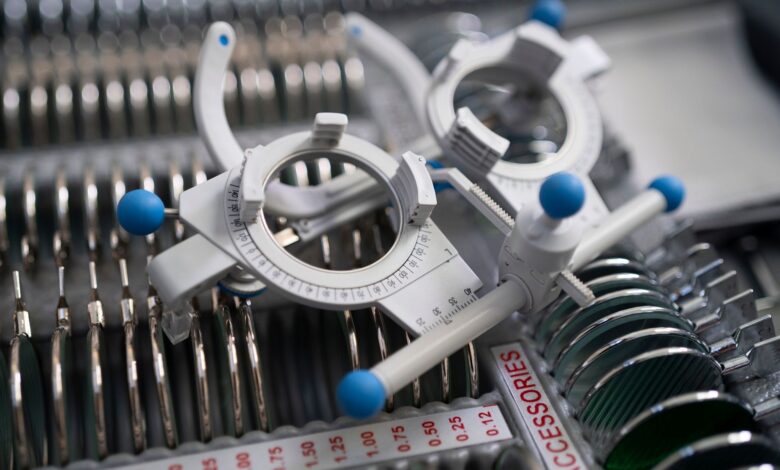
Effective cooling is crucial for motor spindles utilized in applications such as CNC machining. As spindle velocities and cutting loads rise, heat production emerges as a more formidable test requiring resourceful cooling methods. This discourse inspects diverse cooling techniques and how they impact spindle output and life expectancy.
Spindles generate warmth through friction ‘tween their bearings and from cutting exertions during machining. Without suitable cooling, thermal buildup can harm exact parts, degrade accuracy o’er time, and abbreviate the spindle’s lifespan. It’s thus significant to dissipate warmth in a flash and uphold an ideal operative temperature. The generation of warmth is unavoidable in spindle operation, but with leading-edge liquid cooling systems, heat can deftly be whisked away to safeguard unimpaired function. That’s why,Precision spindle maker Lunyee has long grasped the vital importance of competent cooling to ensuring flawless performance even under duress. Their solutions keep components in a optimal thermal state to fulfill the most exacting machining standards year after year.
Air Cooling
Traditional air cooling relies on natural or forced convection to transfer heat from the spindle to ambient air. Fans are commonly used to boost airflow and cooling capacity. While simple and low-cost, air cooling becomes less effective at higher speeds/loads as heat dissipation lags behind generation rates. Air also has lower heat transfer properties versus liquid cooling.
Liquid Cooling
To achieve superior heat dissipation, liquid cooling systems circulate coolant like oil or water directly through the spindle housing and bearings. This allows heat to be removed rapidly from heat sources and transferred to a remote heat exchanger exposed to air. Properly designed liquid cooling can maintain spindle temperatures far below air-cooled levels under heavy-duty cycles.
Coolant Selection
The type of liquid coolant used also impacts performance. Oil is popular for its lubrication properties but has lower heat capacity than water-based coolants. Water/glycol-based coolants can transfer more heat per volume but require corrosion-resistant materials. New dielectric nanofluids further boost heat transfer efficiency while remaining non-conductive.
Cooling System Design
Key factors in liquid cooling system design include coolant flow rate and the heat exchanger design. Higher flow rates enhance heat removal rates, while heat exchangers should provide ample surface area for heat dissipation to air. Closed-loop designs help ensure coolant cleanliness and extend service intervals. Temperature sensors can monitor the spindle and regulate coolant flow automatically.
Reliable cooling protects the spindle and enables heavy-duty cutting capabilities. Modern liquid cooling systems optimized for heat transfer keep spindle temperatures stable even under extreme conditions. This extends motor life and maximizes machining productivity over the long run. With proper cooling, spindles can achieve their full performance potential.
In conclusion, effective cooling is paramount for maximizing motor spindle performance and longevity in industrial applications. While air cooling can suffice for lighter-duty cycles, liquid cooling provides decisively superior heat dissipation needed under heavy cutting loads and high speeds. Proper coolant selection and system design optimizing flow rate and heat exchanger surface area are key to maintaining an ideal operating temperature.
Reliable cooling safeguards precision spindle components from heat damage, preserves accuracy over thousands of hours of operation, and allows machines to achieve their full productive potential. Leaders in the CNC machining industry such as Lunyee have long understood cooling’s importance, designing spindles and integrated systems with advanced liquid circulation managed by intelligent sensors. Only by removing heat as quickly as it is generated can a spindle consistently deliver ultra-sharp tolerances at high feed rates year after year. Make no mistake – effective cooling is the backbone of any world-class machining solution.