Buying Used Conveyor Rollers: Opportunities and Considerations
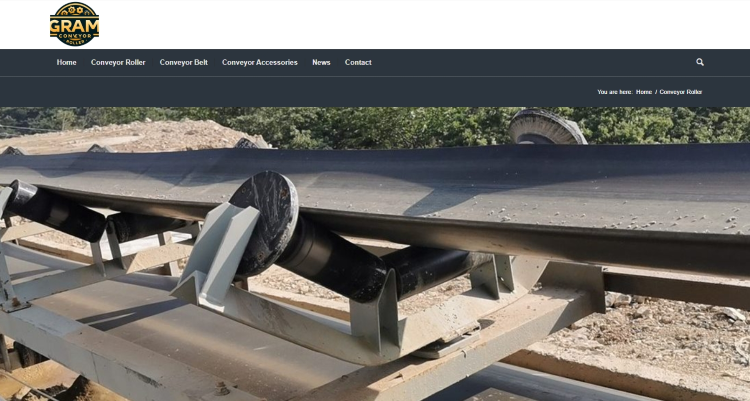
Purchasing used conveyor rollers provides significant economic and environmental benefits, offering businesses an opportunity to save costs and reduce waste. This article explores the opportunities and considerations of buying used equipment, highlighting key factors such as economic advantages, environmental impact, and supplier selection. It also provides practical checklists and questions to ask sellers, ensuring that buyers can identify reliable and compatible rollers that suit their specific conveyor systems. Finally, it addresses potential risks associated with wear and tear, lack of warranties, and compatibility issues, offering mitigation strategies for making the best purchase decisions.
Opportunities and Considerations for Buying Used Conveyor Rollers
In the world of conveyor systems, maximizing efficiency and cost-effectiveness is a significant priority. Buying used conveyor rollers, including specialized options like the Conveyor Impact Roller and Nylon conveyor rollers, can offer economic and environmental advantages. However, these benefits come with specific considerations that must be addressed to ensure a smart purchase.
Economic and Environmental Advantages of Buying Used Conveyor Rollers
- Reduced Initial Costs:
- Lower Purchase Price: The most immediate advantage is the significant reduction in cost compared to new rollers. Used equipment can often be acquired at a fraction of the cost, allowing businesses to reallocate their budgets to other important areas.
- Budget Flexibility: With the savings achieved, companies can invest in supplementary equipment, spare parts, or better quality rollers that enhance operational longevity.
- Depreciation:
- Minimized Value Loss: New equipment rapidly depreciates in value within the first few years, but used rollers have already undergone much of this depreciation. Therefore, resale value remains more stable, offering a better return on investment.
- Availability:
- Reduced Lead Time: Used conveyor rollers are generally ready for immediate purchase and use, bypassing the usual manufacturing and delivery lead times associated with new equipment. This is particularly advantageous in urgent replacement scenarios.
- Environmental Benefits:
- Resource Efficiency: Reusing equipment reduces the demand for new raw materials, minimizing the environmental footprint related to mining, refining, and transportation.
- Waste Reduction: Extending the life of existing equipment reduces the volume of waste sent to landfills, supporting circular economy principles and promoting sustainable business practices.
Considerations Before Purchasing Used Equipment
- Condition Assessment:
- Visual Inspection: Conduct a thorough inspection for signs of wear and tear, such as cracks, rust, or deformation. Even cosmetic damage can indicate underlying issues.
- Operational Testing: If possible, request a demonstration of the rollers in action to check for smooth rotation, noise levels, and stability.
- Compatibility and Specifications:
- Matching Requirements: Ensure that the used rollers match the required specifications of your conveyor system, such as diameter, length, material, and load capacity.
- Conveyor System Compatibility: Confirm that the rollers will fit within the existing framework and are compatible with associated components like bearings and shafts.
- History and Usage:
- Maintenance Records: Request maintenance logs or documentation to understand the frequency and nature of past repairs or servicing.
- Application Type: Learn about the previous application to gauge whether the rollers have been exposed to harsh chemicals, abrasive materials, or extreme temperatures, which could affect performance.
- Supplier Reputation:
- Reliable Vendors: Purchase from reputable suppliers who can provide accurate information about the rollers’ condition and history.
- Warranties and Support: Inquire if the supplier offers any warranty or support services for the used equipment, providing additional security for the investment.
- Compliance and Safety:
- Regulatory Standards: Ensure that the used rollers comply with relevant industry standards and certifications, like ISO or CEMA, for safe and efficient operations.
- Safety Risks: Check for potential safety issues like damaged bearings or compromised seals that could lead to hazardous operational failures.
- Hidden Costs:
- Refurbishing Needs: Account for any costs associated with refurbishing or replacing worn-out components before putting the rollers to use.
- Installation Expenses: Factor in the potential cost of installing used rollers into an existing conveyor system.
By carefully considering these factors, companies can make informed decisions when purchasing used conveyor rollers, benefiting from the cost savings while minimizing the risks involved.
Where to Find Used Conveyor Rollers
Buying used conveyor rollers, including specialized types like Conveyor Impact Roller and Nylon conveyor rollers, can be a smart economic choice if you know where to find quality options and how to verify their condition. Below is an in-depth guide on sourcing and ensuring the reliability of used conveyor rollers.
Sources for Purchasing Used Rollers
Auctions:
- Industrial Equipment Auctions: Many specialized auction houses focus on industrial equipment and machinery. These auctions can be an excellent place to find used conveyor rollers from reputable manufacturers like GRAM Conveyor.
- Bankruptcy and Liquidation Sales: When companies shut down or liquidate, they often sell their conveyor systems in bulk, including rollers. Such auctions may offer equipment at significantly reduced prices.
- Online Auction Platforms: Websites like eBay, BidSpotter, or Ritchie Bros. provide access to global equipment auctions where you can bid on used rollers.
Online Marketplaces:
- Dedicated Industrial Marketplaces: Websites like Machinio, Surplus Record, or EquipNet specialize in second-hand industrial equipment, often providing a wide selection of used conveyor rollers.
- General Marketplaces: Platforms like eBay or Alibaba offer a broader range of sellers, but may require more scrutiny regarding quality and reliability.
Direct from Businesses:
- Manufacturers Upgrading Their Systems: Businesses upgrading their conveyor systems often look to sell their old equipment directly. Approaching such businesses can help negotiate favorable prices on lightly used rollers.
- Refurbishers and Resellers: Some companies specialize in refurbishing used conveyor equipment, offering it with a renewed warranty or quality guarantee. They often buy equipment in bulk, restoring it before reselling.
Industrial Equipment Dealers:
- Dealership Networks: Certain equipment dealers maintain extensive networks to source and resell used conveyor rollers, often providing technical support and refurbishment options.
- Local Dealers: Local industrial suppliers might have connections to used equipment networks and can offer personalized advice.
How to Verify the Quality and Condition of Used Rollers
- Visual Inspection:
- Surface Condition: Examine the rollers for obvious signs of wear, including surface cracks, dents, rust, or significant abrasions.
- Bearing and Shaft Integrity: Check for bearing corrosion, looseness, or misalignment. The shaft should be straight and free of bending or warping.
- Mounting Structures: Assess the integrity of mounting brackets, frames, or housings, which should be structurally sound.
- Operational Testing:
- Rotation and Noise: Rotate the rollers by hand to identify rough bearings, excessive noise, or grinding, which may indicate internal damage.
- Load Testing: If feasible, test the roller under a load similar to your operational conditions to identify its strength and vibration levels.
- Lubrication: Assess whether the roller requires lubrication and if any leaks are visible, indicating potential seal issues.
- Documentation Review:
- Maintenance Records: Request past maintenance logs to understand the frequency and type of repairs performed on the roller.
- Application History: Learn about the conditions in which the roller was previously used, including exposure to chemicals, extreme temperatures, or abrasive materials.
- Manufacturer Specifications: Compare the roller’s current condition to the original manufacturer specifications to identify wear and deterioration.
- Supplier Reputation:
- Reviews and References: Seek reviews, testimonials, or references from previous buyers to gauge the reliability of the seller.
- After-Sales Support: Confirm if the seller offers any after-sales support or warranties that could provide extra protection.
- Compliance Verification:
- Industry Standards: Ensure that the roller adheres to necessary standards like ISO, CEMA, or other relevant certifications.
- Safety Inspections: Verify if the roller has undergone recent safety inspections, ensuring it meets operational safety requirements.
- Expert Consultation:
- Maintenance Professionals: Enlist the help of conveyor maintenance professionals to identify potential issues that may not be immediately visible.
- Roller Manufacturers: Contact the original roller manufacturer for insights on identifying quality and wear issues.
By exploring the right sources and employing a rigorous verification process, you can find reliable, cost-effective used conveyor rollers that meet your operational needs while maximizing your budget.
Risks and Rewards of Buying Used Conveyor Rollers
Investing in used conveyor rollers can lead to significant cost savings but also comes with inherent risks that need careful consideration. Understanding these potential rewards and challenges will enable businesses to make informed purchasing decisions.
Rewards:
- Significant Cost Savings:
- Lower Purchase Price: Used conveyor rollers typically cost less than new ones, offering upfront savings. This reduction in capital expenditure allows for reallocation of resources to other operational needs.
- Bulk Purchasing Discounts: Many suppliers offer substantial discounts on used rollers when purchased in bulk, further reducing costs for larger operations.
- Depreciation Advantage: As used equipment has already undergone initial depreciation, buyers can avoid the steep depreciation curve seen with new equipment, reducing financial losses over time.
- Availability and Quick Turnaround:
- Immediate Availability: Used rollers often have shorter lead times due to existing inventory, which can expedite equipment installation for urgent projects.
- Reduced Downtime: Having access to used rollers in local markets can minimize downtime during unexpected maintenance or repair needs, ensuring production continuity.
- Environmentally Friendly:
- Reduced Waste: Purchasing used rollers contributes to waste reduction by extending the life cycle of functional equipment, reducing the environmental footprint.
- Lower Energy Usage: Manufacturing new rollers requires significant energy and raw materials. Reusing existing equipment conserves energy and promotes sustainable resource use.
- Flexibility in Experimentation:
- Testing New Configurations: Cheaper used rollers can be used to experiment with new conveyor configurations or system layouts without major financial risks.
- Temporary Solutions: For projects with short-term demands, used rollers can provide a cost-effective temporary solution.
Risks:
- Wear and Tear:
- Undetected Damage: Used rollers may have internal damage or fatigue that isn’t immediately visible, which could lead to failure during use.
- Reduced Lifespan: Wear and tear reduce the remaining operational lifespan of used rollers, potentially requiring earlier replacement than new rollers.
- Performance Degradation: Worn rollers may not deliver the same level of performance as new rollers, impacting system efficiency and productivity.
- Lack of Warranty:
- No Manufacturer Guarantee: Unlike new rollers, used rollers often lack a manufacturer’s warranty or guarantee, leaving buyers exposed to financial risk if a roller fails.
- Repair Costs: Without warranty coverage, businesses may incur high repair or replacement costs when used rollers break down, negating initial cost savings.
- Compatibility Issues:
- Model Discontinuation: Older or discontinued models may have different specifications, making them incompatible with current conveyor systems.
- Custom Solutions: Some systems require specialized roller sizes, coatings, or bearings. Used rollers may lack these customizations, necessitating costly retrofitting.
- Compliance and Safety Concerns:
- Obsolete Standards: Older rollers may not meet current safety standards, posing potential risks to workers and requiring additional inspections or retrofitting.
- Non-Compliance Fines: Using outdated or non-compliant equipment can result in regulatory fines or penalties, increasing operational costs.
- Supplier Reliability:
- Unverified Condition: Suppliers might not provide accurate information about the roller’s condition, history, or specifications, leading to mismatched or low-quality purchases.
- Limited After-Sales Support: Some suppliers lack comprehensive after-sales support, leaving businesses without technical assistance in troubleshooting or maintenance.
Mitigating Risks:
- Inspection and Testing:
- Conduct a thorough inspection, including operational testing, to verify the roller’s condition before purchase.
- Consult technical experts to identify potential wear issues and remaining lifespan.
- Sourcing from Reputable Suppliers:
- Choose suppliers with positive customer reviews and established track records in selling high-quality used equipment.
- Prefer suppliers offering limited warranties or after-sales support for used rollers.
- Cross-Checking Specifications:
- Verify that the roller’s specifications match the requirements of your conveyor system to avoid compatibility issues.
- Reach out to the original manufacturer for guidance on compatibility with newer conveyor systems.
- Consider Partial Refurbishment:
- Refurbish certain components to extend the roller’s lifespan and improve performance.
- Combine used and new rollers in strategic locations to balance cost savings with performance.
By carefully weighing these risks and rewards and implementing mitigation strategies, businesses can enjoy significant savings and sustainability benefits when purchasing used conveyor rollers without compromising efficiency and safety.
Making the Right Purchase: Buying Used Conveyor Rollers
Purchasing used conveyor rollers can save money and reduce environmental impact if the right steps are taken. However, to ensure you acquire reliable and suitable equipment, conducting thorough inspections and asking the right questions is essential. Here is a comprehensive guide to inspecting and questioning sellers when buying used rollers.
Checklist for Inspecting Used Conveyor Rollers
- Shaft Integrity:
- Straightness: Roll the shaft on a flat surface to check for warping or bending. A bent shaft can lead to misalignment and increased wear.
- Corrosion and Cracking: Inspect for rust, pitting, and cracks, especially around welded or bolted joints, which can weaken the structure.
- Rolling Surface Wear:
- Uniformity: Examine the roller surface for uneven wear, flat spots, or grooves that can affect performance and tracking.
- Surface Damage: Look for chips, cracks, or gouges that could impact conveyor belt integrity or cause material contamination.
- Bearing Condition:
- Smooth Rotation: Manually rotate the roller to detect bearing resistance, grinding noises, or stiffness, indicating wear or lack of lubrication.
- Bearing Seals: Inspect seals for damage or deterioration that could allow contaminants inside, leading to early bearing failure.
- Mounting Hardware:
- Brackets and Fasteners: Check for damaged, bent, or missing mounting hardware. Loose brackets can cause roller misalignment or vibrations.
- Attachment Method: Verify if the mounting system matches your conveyor framework.
- Coating and Material:
- Surface Coating: Evaluate the surface coating for peeling, blistering, or damage. The coating should match your industry needs (e.g., corrosion resistance or hygienic coating).
- Material Integrity: Ensure that the material (steel, nylon, rubber, etc.) is suitable for the load, environment, and speed required.
- Manufacturer Labels and Identification:
- Model and Serial Numbers: Ensure labels are intact and check model or serial numbers to verify specifications and compatibility.
- Manufacturer Documentation: If available, request the original manufacturer’s documentation, including maintenance records.
Questions to Ask Sellers
- Operational History:
- Previous Usage: Ask what materials were conveyed, the environment (e.g., wet or dusty conditions), and frequency of use to gauge wear and tear.
- Production Capacity: Understand the load and speed demands placed on the roller in its previous application.
- Reason for Selling:
- System Upgrades: If the seller upgraded their conveyor system, the used rollers might still have significant usable life left.
- Wear or Damage: Inquire if specific issues, like bearing failure or shaft bending, prompted the sale.
- Maintenance and Repairs:
- Maintenance History: Request maintenance logs, including lubrication schedules, alignment checks, and bearing replacements, to assess care levels.
- Repaired Components: Identify if any repairs were performed and whether original or aftermarket parts were used.
- Compatibility and Specifications:
- Dimensions: Confirm diameter, length, and shaft diameter against your conveyor’s requirements.
- Industry Standards: Verify the roller meets standards like ISO, CEMA, or FDA (for food processing).
- Warranty or Return Policy:
- Limited Warranty: Ask if any form of limited warranty or guarantee is offered for the used roller.
- Return Policy: Clarify the return policy in case the roller is found incompatible or faulty upon inspection.
- Availability of Replacement Parts:
- Bearings and Seals: Ensure spare parts like bearings, seals, or shafts are readily available for future maintenance.
- Custom Features: Identify if specialized parts like unique coatings or sprockets can be sourced.
By following this checklist and asking these targeted questions, you can make a more informed decision when buying used conveyor rollers, ensuring reliability, compatibility, and performance while minimizing risks associated with pre-owned equipment.